Modernisation of grinding machines
Fit for present and future challenges
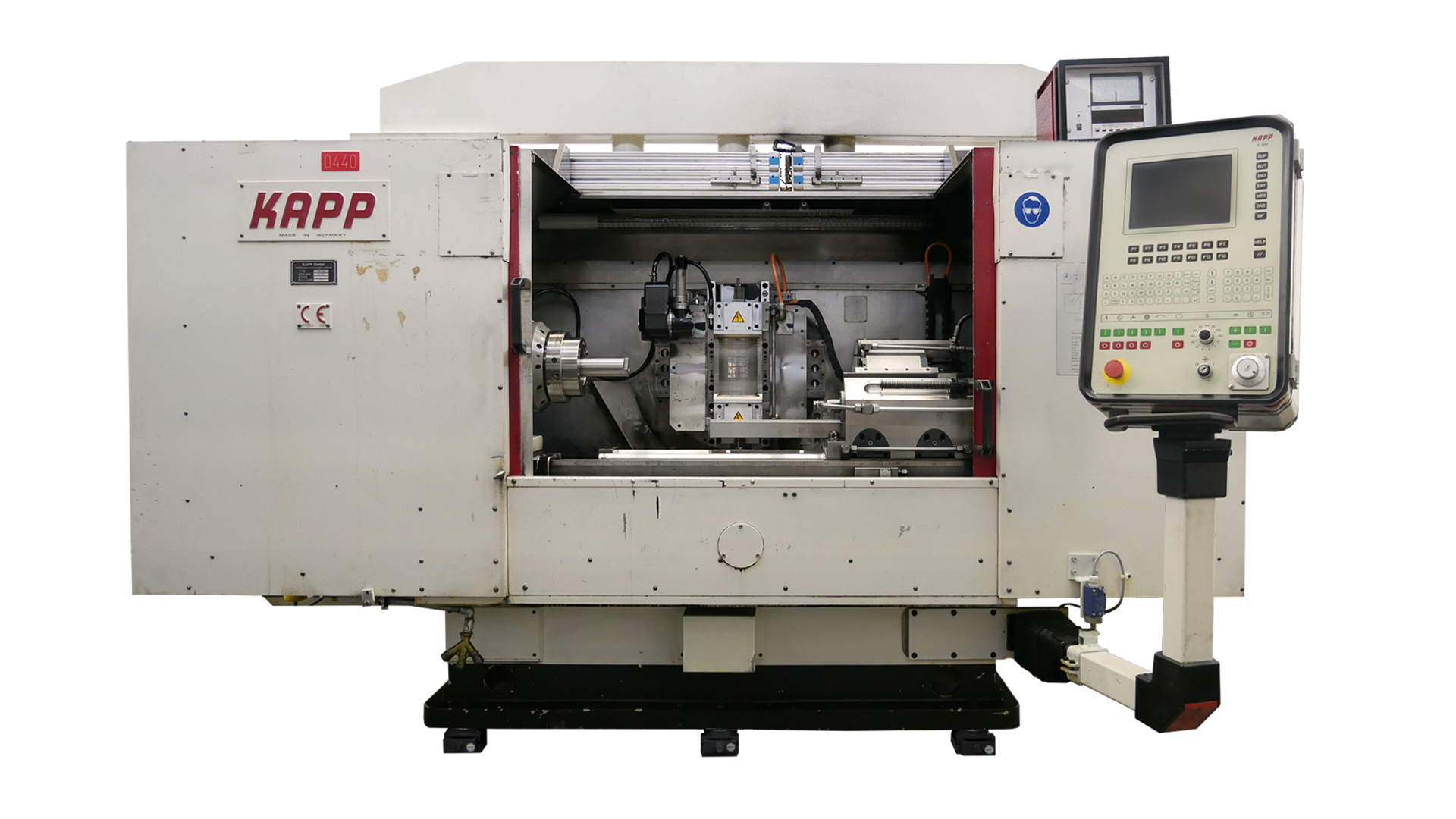
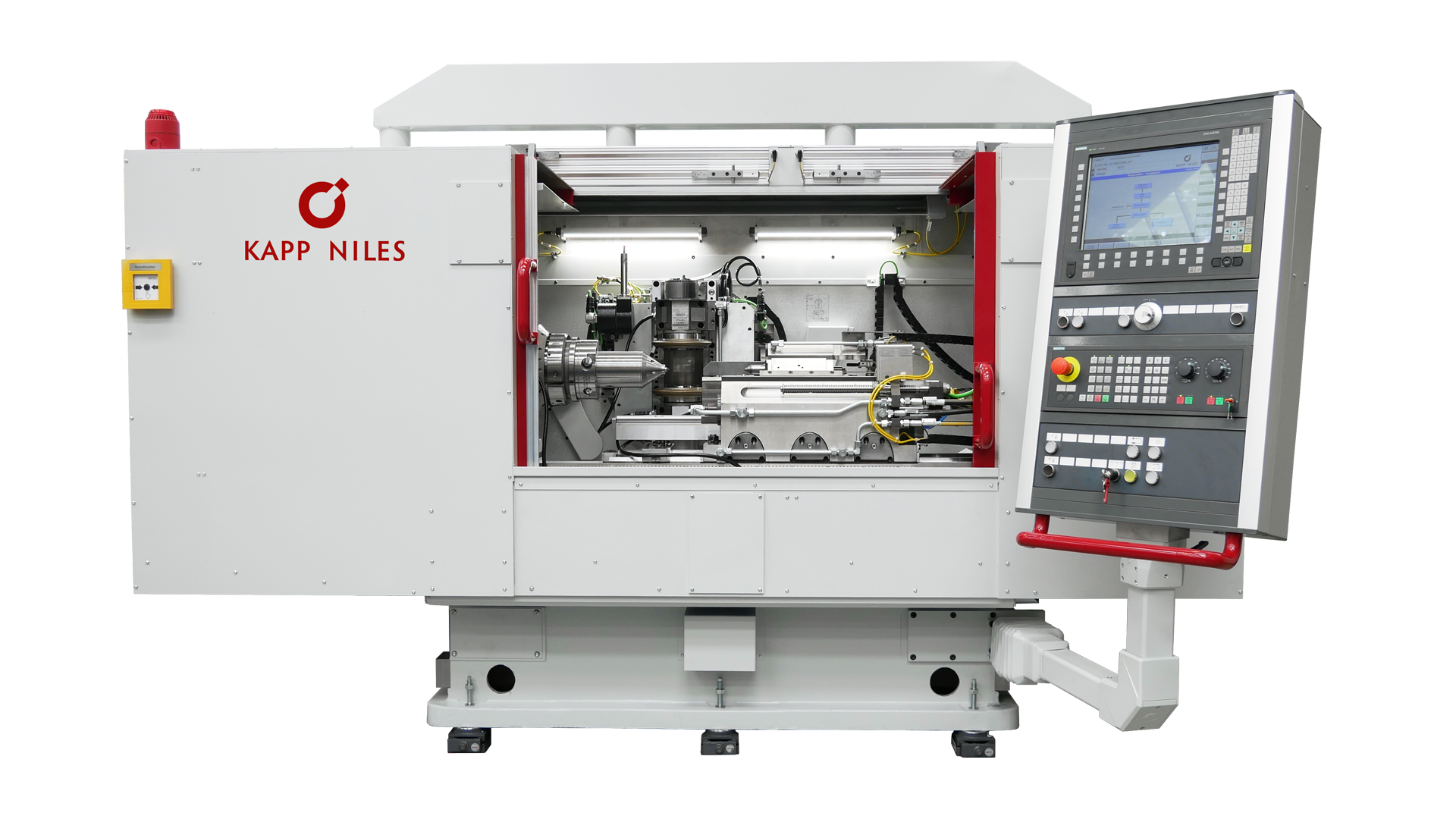
Over time, every grinding machine is subject to operational wear. Unscheduled repairs and the increasingly difficult supply of spare parts, especially for electrical components, can have a significant impact on operation. In extreme cases, the failure of crucial components can bring the entire machine to a standstill and make reliable production planning virtually impossible.
With KN Retrofit and KN Recontrol, your machine is brought up to the latest state of the art and made fit for future requirements. At an investment cost of just 40-65% of a comparable new machine, we comprehensively upgrade your machine in the fields of control, drive and safety technology. This not only leads to a significant extension of the service life, but also to a noticeable increase in oper-ating efficiency.
Our modernisation solutions offer an economical and resource-saving alternative to purchasing a new machine and contribute to long-term operational reliability.
What are the advantages of modernisation?
- Reduction of production costs by improving energy efficiency, productivity and product quality
- Restoring the availability of spare parts
- Preparation for the recording of process and machine data for Industry 4.0
- Resource-saving and economical alternative to a new machine
What are the advantages of KAPP NILES modernisation compared to third-party retrofits?
- Mechanical engineering and software developments from current KAPP NILES machine series
- Reduction of machine downtime to an absolutely necessary minimum
- Renewal of machine documentation
- Extensions of equipment and functions
For which machine / control types are the modernisation solutions available?
- VX / VAS / VIS / VUS (5 axes concept)
- RX / RNS (5 axes concept)
- KX 300 (P), KX 500 FLEX, etc.
- Machine control type OPTRONIC D200
- Machine control type OPTRONIC D300
- Machine control type Siemens 840D Powerline
Comparison of modernisation solutions
KN Retrofit | KN Recontrol | |
---|---|---|
Scope |
|
|
Field of application |
|
|
Advantages |
|
|
Scope of services |
|
|
Results |
|
|
Machine replacement |
|
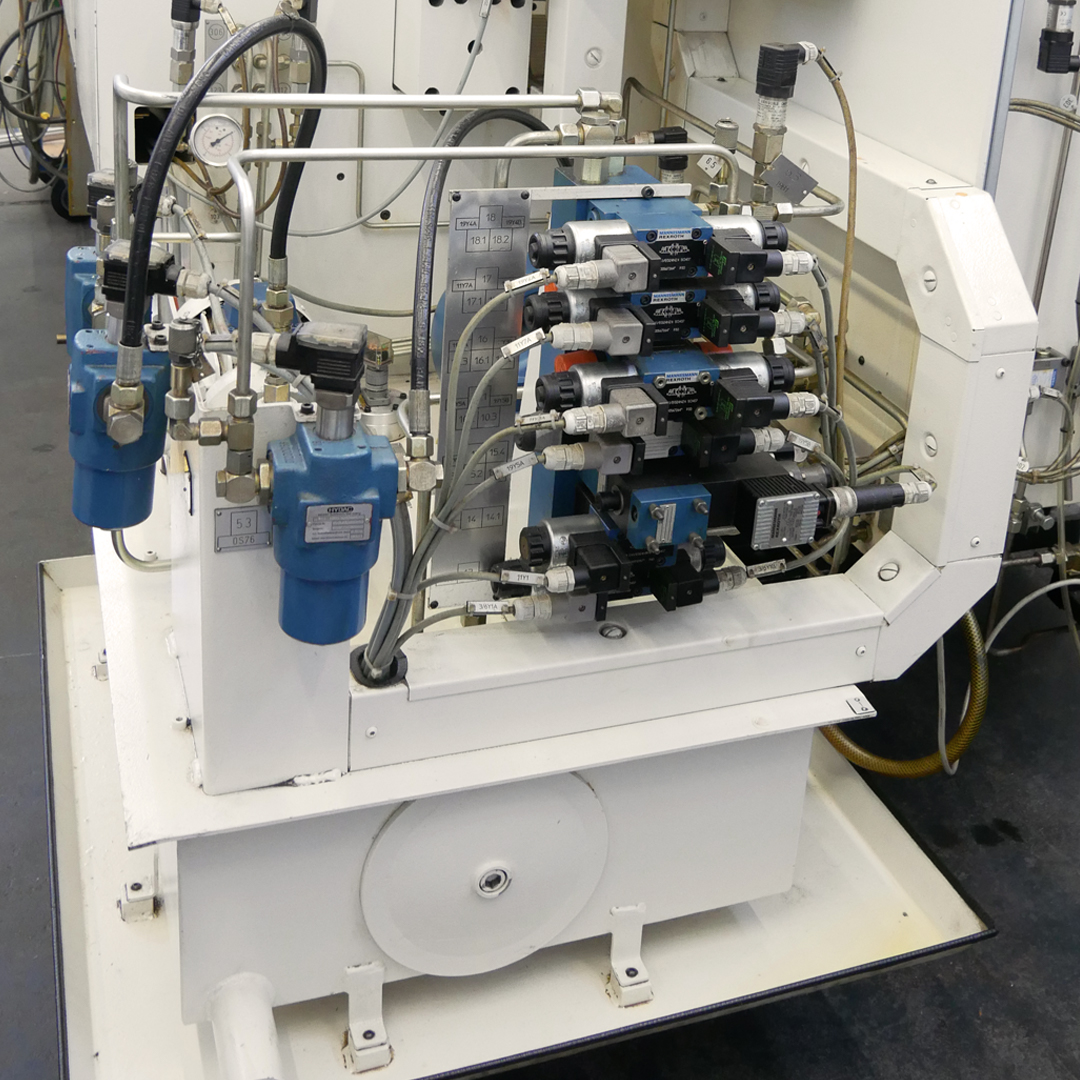
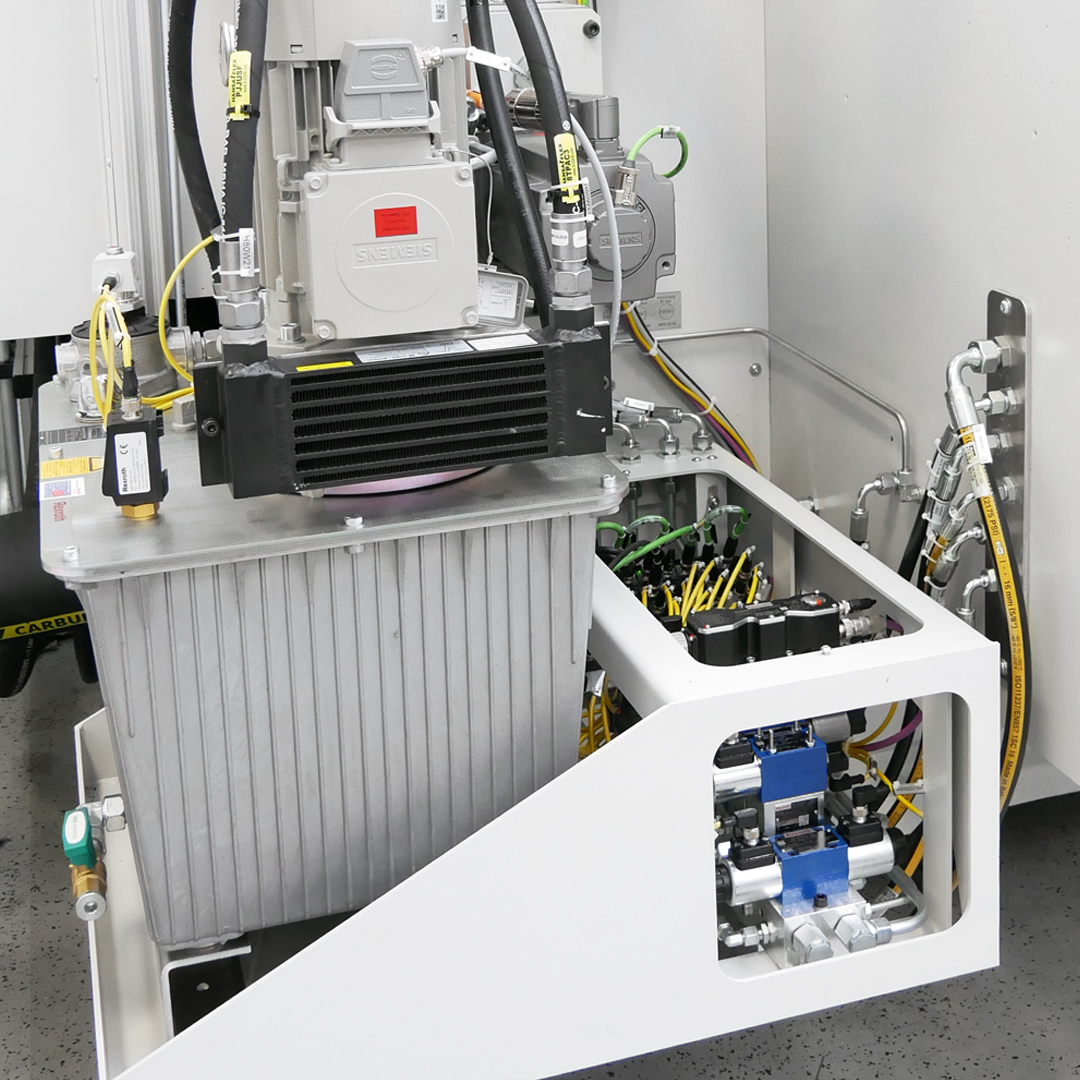
New hydraulic unit
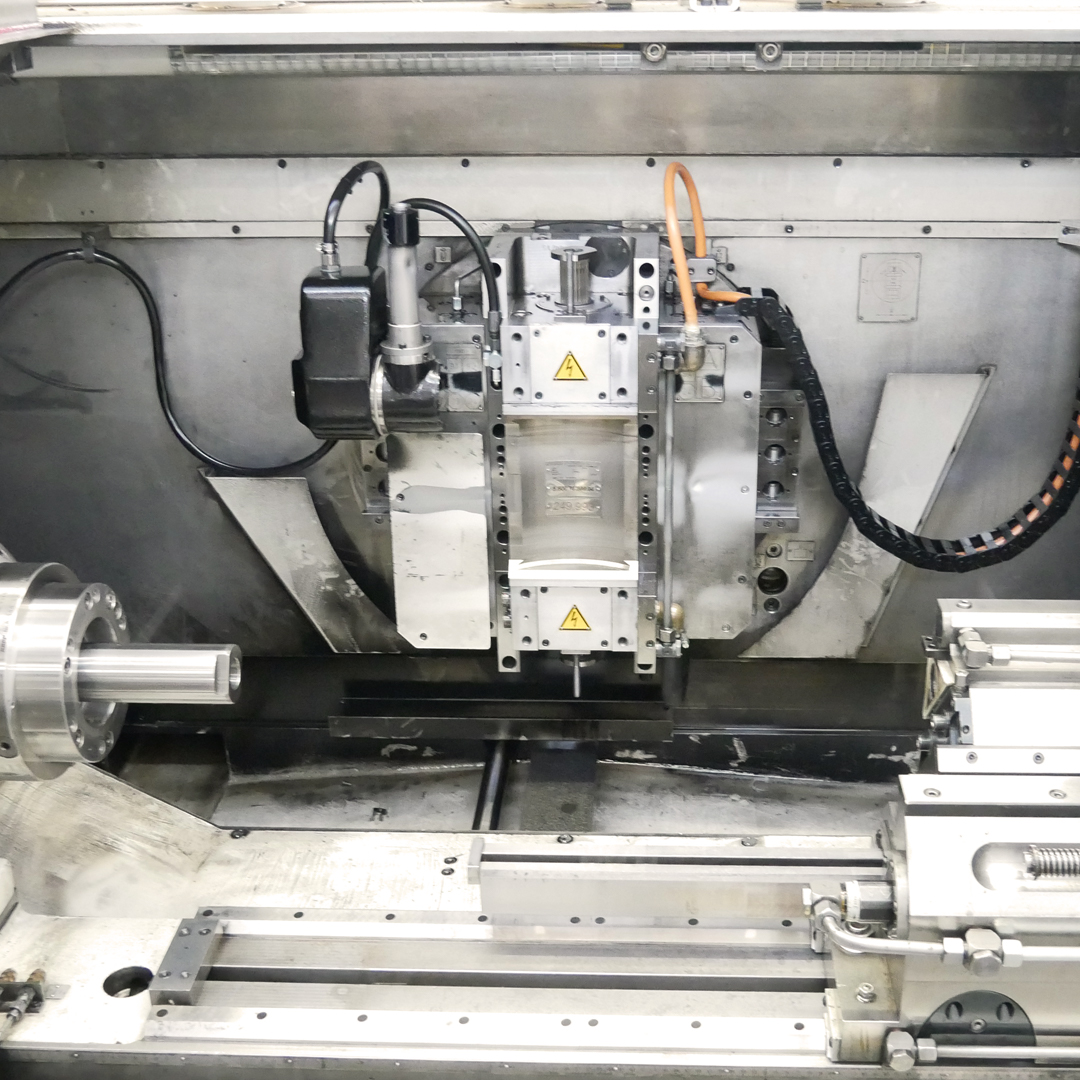
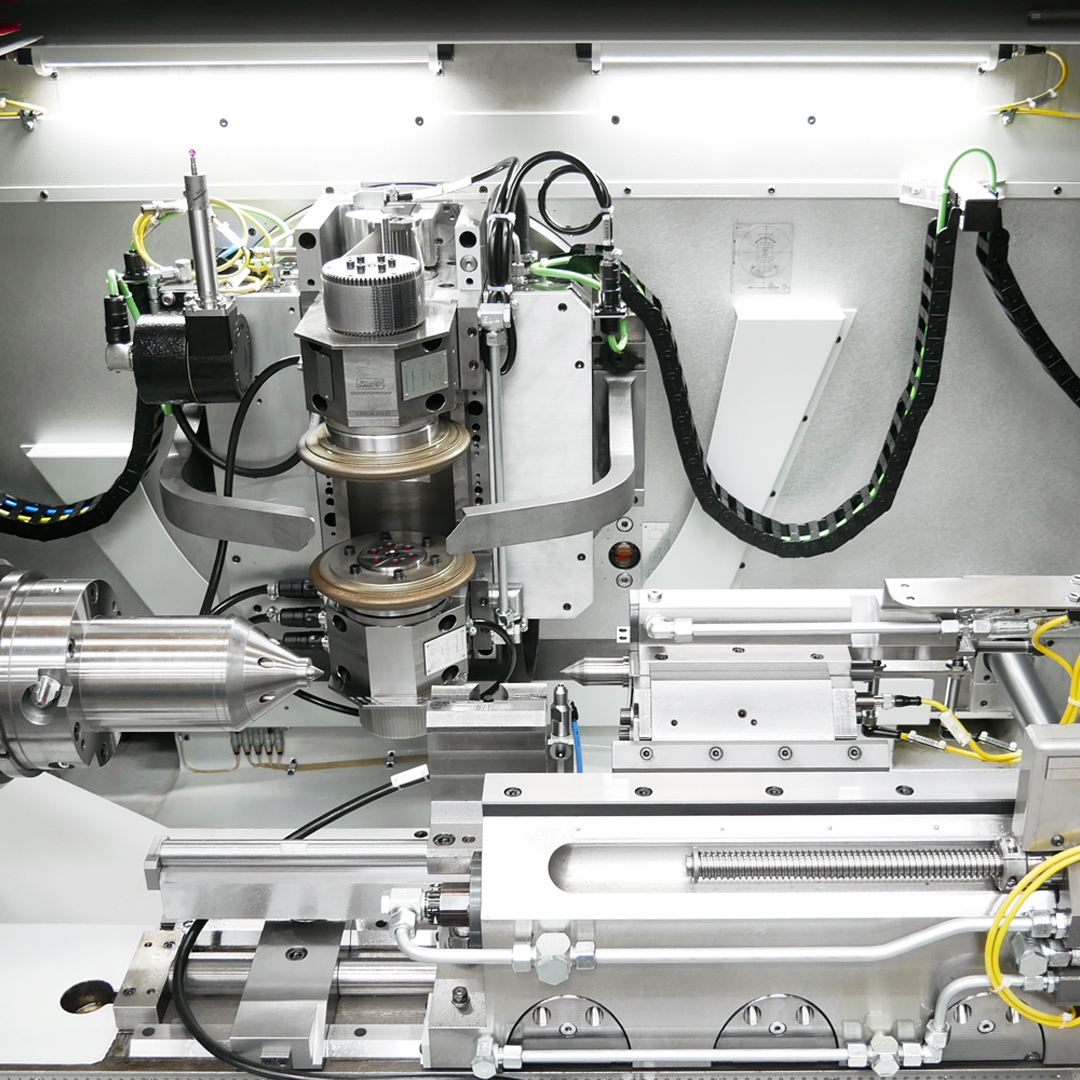
Overhauled machine base
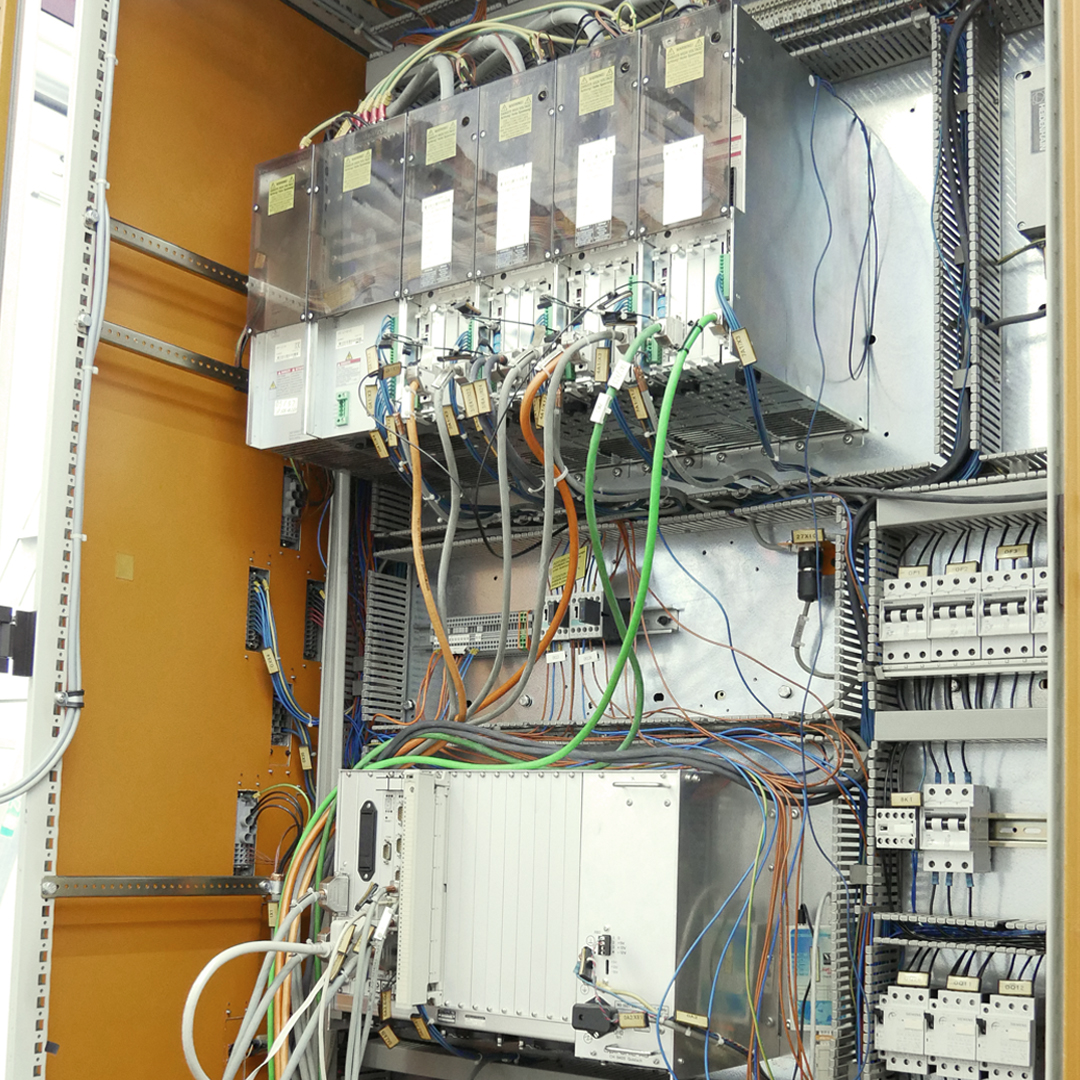
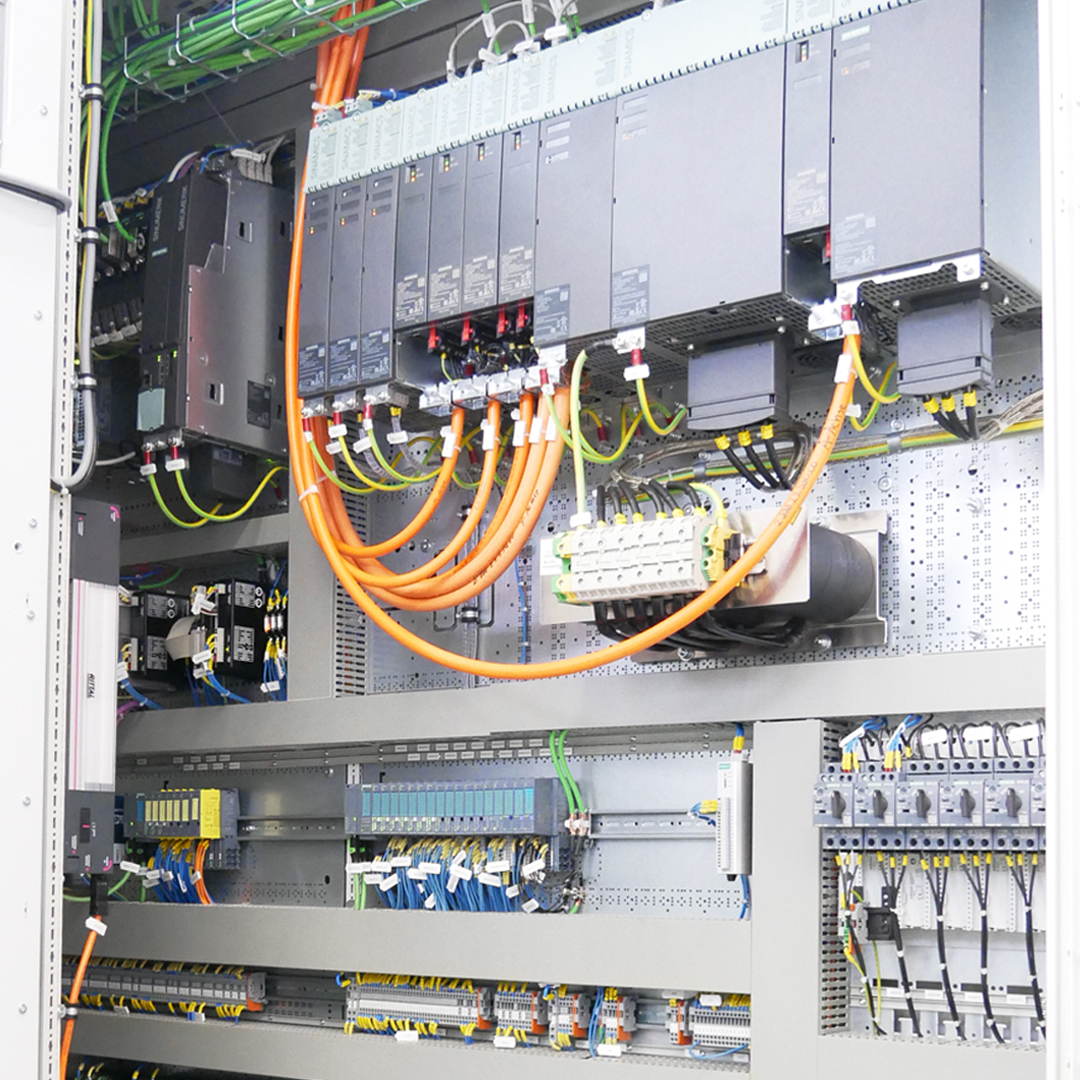
New control technology
Contact person
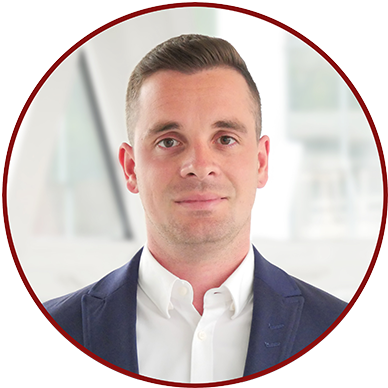
Simon Brückner
📞 +49 9561 866-1364
✉ simon.brueckner@kapp-niles.com
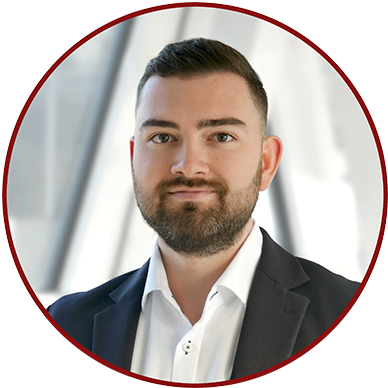
Tim Eckardt
📞 +49 9561 866-1329
✉ tim.eckardt@kapp-niles.com